The efficient and safe transport of liquids and gases is crucial to daily operations in industrial environments. This is where the specialized skills of pipefitters come into play. Pipefitters are responsible for installing, maintaining, and repairing piping systems essential to various industries, from manufacturing to energy production. In this blog, we’ll break down pipefitters’ key roles and responsibilities in industrial settings, explore the challenges they face, and highlight the skills needed to succeed in this vital trade.
1. What Do Pipefitters Do in Industrial Settings?
Pipefitters are highly trained professionals who install and maintain complex piping systems to transport fluids and gases within industrial facilities. These systems can carry anything from water and steam to hazardous chemicals, and their proper installation and maintenance are crucial for safety and efficiency.
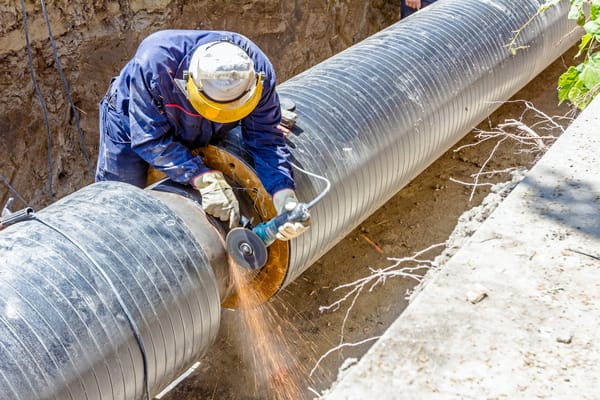
Key Responsibilities of Pipefitters:
- Installation of Piping Systems: Pipefitters work from blueprints or technical drawings to install pipes and ensure they are correctly fitted and aligned within the industrial facility.
- Maintenance and Repair: Regular inspection, maintenance, and repair of piping systems are crucial to prevent leaks, corrosion, and other issues that could disrupt production or cause safety hazards.
- Welding and Fabrication: In many cases, pipefitters are also responsible for welding pipes together and fabricating custom piping solutions for specific industrial needs.
- Testing Systems: After installation or repair, pipefitters test the piping systems for leaks, pressure resistance, and operational functionality to ensure everything works properly.
2. Importance of Pipefitters in Industrial Safety
The work of pipefitters directly impacts the safety of industrial settings. Faulty piping systems can lead to leaks, fires, or even explosions, particularly when dealing with hazardous materials. Pipefitters are crucial in preventing these accidents by ensuring the systems are installed correctly and functioning efficiently.
Safety Responsibilities:
- Pressure Testing: Pipefitters perform pressure tests to ensure piping systems can handle the required loads without breaking down.
- Handling Hazardous Materials: Pipes often carry dangerous chemicals or gases in industrial settings. Pipefitters are trained to install and maintain systems to safely transport these materials.
- Compliance with Safety Standards: Pipefitters must adhere to industry safety standards, including the Occupational Safety and Health Administration (OSHA) regulations, to ensure their work is compliant and safe for workers and the environment.
3. Key Skills Required for Pipefitters
Pipefitters require a diverse skill set to handle the demands of industrial environments effectively. Their job requires both technical knowledge and hands-on expertise.
Essential Skills for Industrial Pipefitters:
- Technical Blueprint Reading: Pipefitters need to be able to read and interpret complex blueprints and technical diagrams that outline the design and layout of piping systems.
- Precision and Attention to Detail: Installing and maintaining piping systems requires precision to ensure proper alignment, secure connections, and compliance with safety regulations.
- Welding and Fabrication: Pipefitters must have welding skills to assemble pipes and other components securely. Custom fabrication may also be required when pre-made parts don’t meet the specifications.
- Problem-Solving: Industrial settings often present unique challenges, and pipefitters must be adept at troubleshooting issues during installation or maintenance.
4. Types of Piping Systems in Industrial Settings
Industrial facilities have several types of piping systems, each serving a specific purpose. Pipefitters need to be familiar with the different systems they may work on.
Common Types of Piping Systems:
- Process Piping: This type of piping transports liquids, chemicals, or gases used in manufacturing processes. Proper installation is critical for maintaining production efficiency.
- Steam Piping: Many industrial facilities use steam for heating or as part of their manufacturing processes. Steam piping must be properly insulated and capable of handling high temperatures and pressure.
- Utility Piping includes piping that transports water, air, or natural gas to power machinery or provide basic utilities within a facility.
- Sanitary Piping: In industries like food and pharmaceuticals, sanitary piping is essential for transporting products safely and preventing contamination.
5. Challenges Faced by Pipefitters in Industrial Settings

Pipefitters often face unique challenges in industrial settings due to the complexity and scale of the systems they work on. These challenges require a high level of expertise and adaptability.
Common Challenges:
- High-Pressure Systems: Many industrial processes use high-pressure systems that require careful handling and precise installation to avoid accidents or system failures.
- Working in Hazardous Environments: Pipefitters frequently work in environments that involve dangerous chemicals, extreme temperatures, or confined spaces, which requires strict adherence to safety protocols.
- Maintaining System Efficiency: Industrial piping systems can degrade over time due to wear and tear, corrosion, or sediment buildup. Pipefitters must ensure systems remain efficient and operational, often requiring quick repairs to minimize downtime.
6. Training and Certification for Industrial Pipefitters
Becoming an industrial pipefitter requires specialized training and certification, which ensures that workers have the necessary skills to perform their duties safely and effectively.
Training Path:
- Apprenticeships: Many pipefitters start their careers through apprenticeships, receiving hands-on training while working under experienced professionals.
- Certification Programs: Pipefitters can obtain certification in various specialized areas, such as welding, high-pressure systems, or handling hazardous materials. Certifications from recognized organizations, such as the National Center for Construction Education and Research (NCCER), enhance credibility and job prospects.
- Ongoing Education: As technology and industry standards evolve, pipefitters must continue their education to stay current with new techniques, safety protocols, and industry regulations.
The Vital Role of Pipefitters in Industry
Pipefitters are indispensable in keeping industrial facilities running smoothly, ensuring critical piping systems function efficiently and safely. Their expertise in installing, maintaining, and repairing these systems is essential to the production process and the overall safety of the workplace. As industries grow and evolve, the demand for skilled pipefitters rises, making this a crucial and rewarding career in industrial settings.